All About Crimping
Q. I have had a few failures with crimp tubes sliding off or breaking. Is there something that I am doing wrong?
A. Usually when people have trouble crimping, it's because the crimps are too big for the wire. You want the wire to fill as much space inside the crimp as possible, so it may be necessary to change to a smaller sized crimp or a larger sized wire. We have a crimping tutorial where you can see the proper crimping technique (below).
Keep these tips in mind:
• The inventor of the crimp tool recommends using a three-step method:
1. Place the crimp inside the outer jaws and squeeze gently to form an oval-shaped crimp.
2. Place the crimp inside the inner jaws and squeeze hard to crease the crimp across the center.
3. Turn the crimp 90-degrees and place it inside the outer jaws. Squeeze gently to fold and round the crimp.
• Make sure the wires are parallel inside the crimp. Wires that cross can prevent the crimp from creasing properly in Step 2.
• If you are crimping onto a single wire such as in an illusion design, place the wire to one side inside the crimp before using the crimping tool.
• It may be necessary to switch to a larger diameter of wire. Crimps work better when the wire fills the crimps as much as possible.
Does Beading Wire Stretch?
Q. Most of my bracelets and necklaces are stretching out - up to 1/2" or so. I am making combinations of glass beads, seed beads, crystals and sterling silver. When I first make a piece, the beads are nice and tight. Within a month or so, there is a noticeable gap at the ends. What is going on?
A. Since the wire is made of stainless steel, what you are experiencing is not "stretching" but rather the strands are becoming untwisted, very similar to the way silk cord can untwist when under pressure. This is either a result of using a diameter of wire that is too small or stringing your beads too tightly. First, check to make sure that you're using the largest diameter of wire that will pass comfortably through the beads. If the size of wire you're using is already filling the bead holes as much as possible, then your designs are probably just too tight. You can remedy this problem by using Bead Bumpers, which are tiny, stretchy beads that you can use at the ends or within the pattern. They are slightly squish-able so you can get the "nice and tight" look while giving the beads and wire a little more space.
Silver Beadalon Wire Explained
Q. What is the difference between sterling silver and silver-plated Beadalon wire?
A. Sterling silver Beadalon wire is soft, flexible and made of pure .925 sterling. This wire is for the purist beader who requires high flexibility and precious metal quality. A thin, smooth layer of crystal clear nylon covers this wire to prolong strand life and prevent kinking. The beauty of this fine wire is unsurpassed by any other beading wire on the market. Due to its extreme softness, we recommend reserving .925 Solid Sterling Wire for your finest quality, most precious designs. For extended-wear designs, we recommend using our stronger, more abrasion-resistant silver-plated wire or value-priced silver color wire.
Preventing Wire Breakage
Q. I'm new to beading and would like to know why some of my necklaces and bracelets break in the center. They are made of semiprecious gems, glass and silver.
A. Breakage is typically caused by abrasion on the wire. The kinds of beads you're can be sharp on the inside and can cut through the wire over time. We always recommend using a bead reamer to smooth any rough spots inside the bead holes. (A bead reamer is a round file that fits inside the bead hole.) You should also use the largest diameter of wire that will fit through the bead holes. This will reduce the amount of friction inside the bead, thus reducing the potential for abrasion. Beadalon 49 is the most flexible wire, so it should always be used for jewelry that is going to get a lot of wear and tear, such as bracelets. Also, remember that it's important to maintain some "play" in your designs and don't string them too tightly.
Using Scrimp® and Wire Guardian™ Findings
Q. I find that when I string heavier lampwork beads, the crimps sometimes fail. Exactly how secure is the Scrimp finding compared to a crimp beads or tube? Also, what is a Wire Guardian finding?
A. A Scrimp finding is actually more secure than a traditional crimp because the set-screw holds the wire in place inside the finding without creating any sharp edges that can cause wire breakage. Scrimp findings have the added advantages of being removable and reusable. To use a Scrimp finding, just partially unscrew the screw inside the finding, insert Beadalon wire into the finding, through the clasp, and back through the Scrimp finding. Use a Wire Guardian finding where extra abrasion is likely to occur. It's a small U-shaped piece of hollow wire that protects the beading wire where it meets the clasp. You can use a Scrimp finding without the Wire Guardian finding but the combination makes the connection as durable as possible.
Finishing Memory Wire
Q. I am new to bead stringing and have just started exploring memory wire. If I make a necklace, what is the best way to end it? I have seen some necklaces that have a round end glued onto the tips. Is this secure enough?
A. Since memory wire is tempered to "remember" its shape, it isn't necessary to use a clasp. Use memory wire shears (memory wire will ruin ordinary wire cutters) to cut at least 1 ½ loops of memory wire, so the ends will overlap on the neck when worn and prevent the necklace from coming off. Memory Wire End Caps come in different shapes and add a nice, professional finish to the ends. Use a piece of sandpaper to lightly sand the ends of the memory wire, then place a drop of epoxy or BeadFix glue on the end of the wire and press an end cap onto the wire. String a few beads, and then spot-glue the last few beads together to help hold the end cap in place. For a glue-free design, you could use a special Memory Wire Scrimp finding instead. It has the added advantage of being removable and reusable.
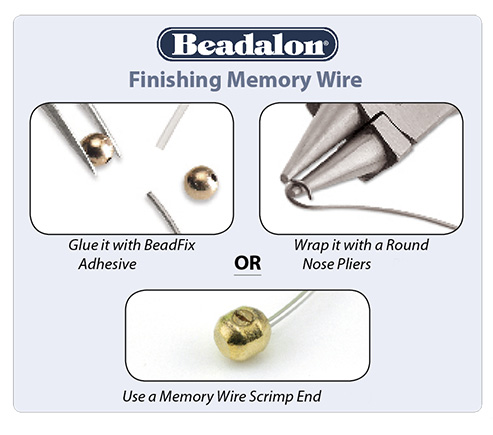
Knotting Elasticity
Q. I purchased a spool of Elasticity 0.8mm and no matter what I try, I cannot get the product to hold a knot. Any suggestions?
A. The knot is recommended for elasticity (see Right). We recommend stretching the cord as you tie it to create a little bit of tension. Add a drop of Beadalon Bead Stringing Glue or jeweler's cement to the knot and let it dry before cutting off any extra cord. After the glue dries, tuck the knot inside the closest bead hole if possible.
Using Wire Looping Pliers
Q. I have one of your wire looping tools but I can't figure out how to use it. I'm trying to loop standard size headpins to make prettier loops for earrings and dangles. Help!
A. The real advantage of the looping pliers is that you can use the graduated tip of the pliers to make consistently sized loops and jump rings. To make a dangle, string some beads onto a headpin. Bend the headpin in a right angle against the top bead. Make sure you're holding the bead so the wire is parallel to the floor, and then place the round part of the plier jaws on top of the wire and roll them back toward the bead to make a nice, clean loop.
Wire Wrapping Suggestions
Q. What kind of wire do you recommend as an alternative to sterling silver for wire wrapping?
A. Beadalon carries a variety of wire for wire wrapping, including a new German-style silver plated wire that looks and feels like sterling without the cost. It comes in the three of the most popular sizes for wire wrapping: 20, 22 and 24-gauge. The size you choose will depend on what you're doing with it. 20-gauge is best for things that must hold their shape like eye pins, 22-gauge is a good all-purpose size for making wire-wrapped bead links, and 24-gauge is best for wrapping smaller or more delicate beads such as freshwater pearls.
Cutting Dandyline™ Thread
Q. I have tried using Nymo for my beadwork, but I find that it frays and knots easily. I thought I would switch to Dandyline because it seems like it would be stronger and easier to work with. But, how do you cut it? I cannot seem to get a clean cut.
A. Dandyline is made of tightly woven Spectra® thread, so it is very strong for its diameter. The fibers are so tightly woven and so abrasion resistant that it is difficult to cut with regular scissors but those same features make it great for jewelry making. There are two methods that you can use to cut Dandyline. Either use a very sharp wire nipper, or run the thread down the open blade of a pair of scissors. (You'd think it would fray, but it doesn't!)
The Advantages of WildFire™
Q. I do a lot of bead weaving and I'm looking for a thread that is very strong. Would WildFire be the best choice?
A. Wildfire combines the strength and durability of Dandyline with a smooth, thermally bonded coating to create a superior stringing product that cannot be pierced with a needle. This is particularly advantageous for bead weaving because you won't split your thread when passing multiple times through the beads. It's super strong, zero stretch, waterproof, the color won't come off on your hands, it will not fray at the ends and it's easy to string on a needle.
Using a Spin-N-Bead™
Q. I just bought a Spin-N-Bead but I can't make it work. Do I need a special type of needle? What's the secret?
A. It's recommended that you use a Curved Big Eye Needle with the Spin-N-Bead. They are sold separately or you can make your own by bending a regular big eye needle in a curved "J" shape. Hold the needle in your dominant hand and dip the bent tip of the needle into the beads pointing the tip slightly outward toward the wall of the bowl but with the tip generally pointing back toward yourself. Use your non-dominant hand to spin the bowl away from yourself so the needle is pointing against the flow of the beads. The beads should jump onto the needle. You may need to adjust the position of the needle a little bit until the flow starts happening. It works best if the bowl is pretty full of beads and you can just skim the surface with the needle. Fill up the needle with beads, push them onto the thread, and then fill the needle up again.
French Wire Explained
Q. I have a knotted necklace pattern that calls for 1/2" of French wire. I have never used French wire and don't know anything about it. Do I really need it?
A. Also known as "bullion" or "gimp," French wire is a tiny, coiled wire that covers beading thread where it meets the clasp. It protects the thread from abrasion and makes the design more durable. It is available in different diameters that you choose based on the diameter of the thread. It comes in one long piece, which you cut into smaller lengths. Choose from sterling silver, silver-plated, or gold-plated finishes.
Making ID Badge Lanyards
Q. I am looking for a pattern to make a bead lanyard and I thought maybe you might be able to help me. Do you have any instructions or tips?
A. Here are instructions for a basic badge lanyard:
1. Cut a 40" length of Beadalon 49-strand wire in the .024" diameter or the largest diameter that will pass through the bead holes.
2. String badge clip onto center of wire.
3. String beads as desired on each side of badge clip.
4. To finish the ends, use two crimp tubes. Pass each wire end through a crimp tube, string a few last beads and pass the other wire end through the opposite side of the crimp tube and bead section. This will help spread the tension out a little bit and you won't have to rely on just one crimp.
Designing Illusion Necklaces
Q. I have a customer who wants me to make her an "illusion" necklace. I have a general idea how to do it, but I need some guidance from you. What kind of wire do I use and how do I know what measurements to use between the beads?